We use cookies to ensure that we give the best experience on our website. Click here for more information
Crafting a BONZ coat
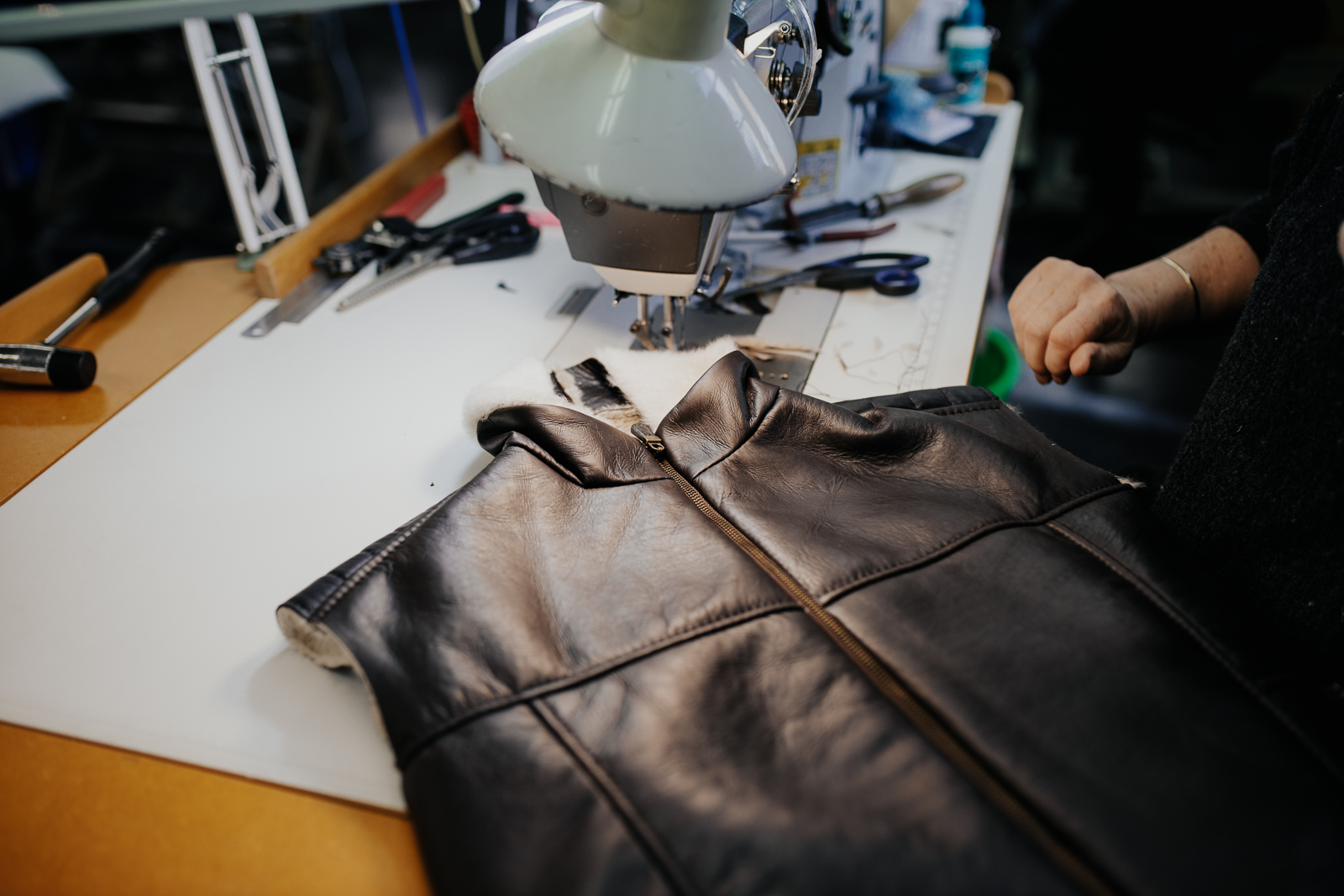
Each BONZ coat represents a true New Zealand artisanal journey, refined over our 50 years of crafting this unique product. From our rolling New Zealand pastures, to the local tanneries and our factory floor, the skills that go into every coat are highly specialised and localised, passed down through generations: they are as unique as the finished product itself. While each component of a BONZ coat has a specialist or craftsperson, the collaboration and enduring Kiwi spirit of our passionate teams is what replicates that BONZ quality standard and drives constant improvement and evolution.
The skills that go into every coat are highly specialised and localised, passed down through generations: they are as unique as the finished product itself.
It all starts with the raw materials. The majority of lambskin used in our garments is called Slinkskin: this rare lambskin is a by-product of New Zealand wool industry, and are the lambs that are either still born, or die within the first few days of life as a result of the cold southern New Zealand weather in Spring (when they are born). We choose to use this material not just due to its ethical and sustainable qualities, but also because the young age of the lambs makes for an incredibly soft double face lambskin that cannot be bested by any other material globally. We hand select the salted slink lambskin pelts from our local Invercargill tannery, and work with them closely to form the colours and finishes of our seasonal collections. With a perfected raw material, it is time for the next step: handcrafting the coat itself.
Handcrafting a coat starts in the design room. We align the finest materials including locally hand selected lambskin, leather, buttons and zips. The slink lambskin does not come on a roll as would mainstream materials, and the skins are a fraction of the size of a traditional shearling lambskin or cow hide, so a complex pattern is required, with some coats having upwards of 150 individual panels. The designers builds this commercial disadvantage into the product. The smaller panel size allows for greater control over shape and fit. It also provides the ability to repair and replace panels from older coats. Once design has been finalised, a pattern will be cut manually for each size and transported to our cutting room for production.
The skins are a fraction of the size of a traditional shearling lambskin or cow hide, so a complex pattern is required, with some coats having upwards of 150 individual panels
The first step of coat production is called Match & Mark. It is completed by someone called a ‘Cutter’. As you could gather from the name, this process refers to the matching the lambskins by leather colour and wool structure and then marking any flaws so that the pattern can be laid around them. Each coat will use 20-60 of our small slink lambskins, and for these to match, the cutter will sort through an average of 800 individual lambskins. While this process can be somewhat automated by modern technology, we continue doing it by hand as it ensures that each coat is perfect.
Each coat will use 20-60 of our small slink lambskins, and for these to match, the cutter will sort through an average of 800 individual lambskins.
Once the skin matching and marking has been completed, the cutter will sort pattern onto the chosen skins, moving them around like a jigsaw puzzle to ensure that no imperfections make their way onto a coat. A good cutting yield on the 2-3 square foot slink lambskins is 40%, and the average is 37% - in other words, more than 60% of the slink lambskin cannot be used in the coat. As with sorting, there is technology available to automate parts of this process, however it is not yet able to reach our high quality standards.
The next step is to cut the panels that have been drawn onto the lambskin. This is performed by someone called a Snipper. The snipper will use an air driven spinning cutting tool to perforate the leather side of the lambskin and bring out the panels . Once the panels have all been cut, the Snipper will use a specialised shearing tool to trim the wool on edges marketed on the design notes. The shaved edges make it easier for the machinists to sew the panels together and ensure a higher level of quality on the finished garment. The Snipper will also prepare any leather trims and pocket bags for the garment. The panels, along with the pattern, are then put into a tub and make the way to the machining room – where the magic happens.
The panels and pattern will make their way to a machinists table by way of a runner or transporter. Machinists will generally specialise in only a few styles, ensuring that they are fast, but can also consistently craft to the BONZ quality standards. The most common sewing machines used are known as Walking Foot machines. Because the lambskin is bulky compared to fabrics, the machine foot, which would normally just ride over the fabric has been made into a two-part foot that steps over the skins as it sews. Other commonly used machines, depending on style, are flat locking and cupping machines – each offering a different finish. None of these machines are automated, and the skill and quality output lies with the machinist. Each garment will take upwards of 3 hours just in the machining.
None of these machines are automated, and the skill and quality output lies with the machinist.
After machinists have sewn panels and trims, the nearly completed garment is transferred to the Grooming and Finishing department. The finishing of a garment includes attaching any buttons, rivets or clips as per the design sheet. Our heavy horn buttons are all hand sewn and heat shanked to ensure they last the test of time. Once the garment is completed, the groomer will go over every inch, cutting any remaining loose threads, combing the wool/fur and removing any lint that has come from the production line. They will also press and iron the garments using specialty equipment to remove any creases from the tanning or production line. The groomer also has the job of finding any flaws, and will send a coat back down the production line to be fixed, or panels replaced, should it not meet the BONZ quality standards.
With an stamp of approval from Grooming and Finishing, the garment is transferred to the dispatch team and either sent to one our BONZ retail boutiques, or straight to a customers around the world. The making of your coat is just the beginning. With every new adventure over the years, your lambskin or leather coat will contour to your form, developing more character and becoming part of your journey. The coats will be used for decades, only returning to the factory when well-worn and loved and needing replacement panels or buttons, ready to be passed down to the next generation.
The next step is tanning—a process that is equal parts art and science. Expert tanners use traditional techniques to transform raw hides into beautifully finished leather and sheepskin in a variety of colours and styles. Only the best pelts are selected for the next step: handcrafting the coat itself.
It is with passion and pride that we continue to craft our uniquely ethical and sustainable coats at the very bottom of New Zealand for discerning customers across the globe. We take pride in our heritage, and supporting those working within our companies, and the extended family that work for our companies across our local supply chain.
OSCAR RODWELL, SECOND GENERATION OWNER & CEO , BONZ GROUP NEW ZEALAND